No hay dos placas de circuito impreso estándar iguales. Cada PCB tiene una función única para un producto en particular. Por lo tanto, producir una PCB es un proceso complejo y multifacético. Esta descripción general cubre los pasos más importantes al producir una PCB multicapa.
Cuando ordena PCBs de SprintPCB, está adquiriendo calidad que se paga por sí misma con el tiempo. Esto está garantizado a través de especificaciones de productos y controles de calidad mucho más rigurosos que los de otros proveedores, y asegura que el producto cumpla con lo que promete. El diagrama de flujo de producción a continuación ilustra las formas en que el proceso de SprintPCB es único o va más allá del estándar IPC.
Si no puede encontrar la respuesta que busca o desea más detalles, no dude en ponerse en contacto con nosotros, estaremos encantados de ayudarle.
-
PPE
-
Material issue
-
Inner layer
-
Inner layer etch
-
Inner layer AOI
-
Lamination
-
Drilling
-
PTH
-
Panel plating
-
Outer layer image
-
Pattern plate
-
Outer layer etch
-
Outer layer AOI
-
Via hole plugging
-
Soldermask
-
Surface finish
-
Profile
-
ET
-
Final inspection
-
Packaging
01
PPE - Pre Production Engineering
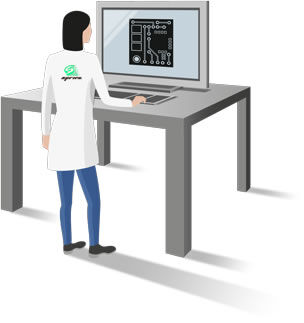
Los datos proporcionados por el cliente (gerber) se utilizan para generar los datos de fabricación específicos para la PCB (artworks para procesos de imagen y datos de perforación para programas de taladrado). Los ingenieros comparan las demandas/especificaciones con las capacidades para asegurar el cumplimiento y también determinar los pasos del proceso y las verificaciones asociadas.
02
Material issue
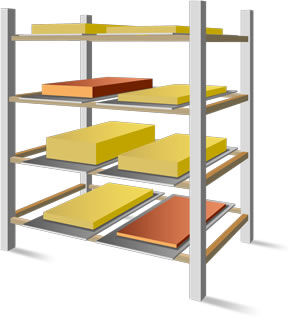
Los materiales de diversos tipos son recibidos de proveedores aprobados y se mantienen en ambientes controlados hasta que se requieran. Utilizando sistemas FIFO, los materiales específicos se liberan para la producción de una orden de compra específica, con los materiales base cortados a los tamaños requeridos. Todos los materiales utilizados pueden rastrearse hasta su lote de fabricación.
03
Inner layer

La Etapa 1 consiste en transferir la imagen utilizando una película de arte a la superficie de la placa mediante un material fotosensible en seco y luz ultravioleta, lo cual polimerizará el material fotosensible expuesto por el arte.
Esta fase del proceso se realiza en una sala limpia.
04
Inner layer AOI

La Etapa 2 consiste en eliminar el cobre no deseado del panel mediante un proceso de grabado. Una vez que se ha retirado este cobre, se elimina el material fotosensible restante, dejando atrás la circuitería de cobre que coincide con el diseño.
05
Inner layer etch

Se realiza una inspección de la circuitría en comparación con las "imágenes" digitales para verificar que coincide con el diseño y que no presenta defectos. Esto se logra mediante un escaneo de la placa y, posteriormente, inspectores capacitados verificarán cualquier anomalía que el proceso de escaneo haya destacado.
06
Lamination

Las capas internas tienen una capa de óxido aplicada y luego se "apilan" junto con prepeg que proporciona aislamiento entre las capas, y se agrega lámina de cobre en la parte superior e inferior del conjunto. El proceso de laminación utiliza una combinación de temperatura específica y presión durante un tiempo determinado para permitir que la resina dentro del prepeg fluya y una las capas para formar un panel multicapa sólido.
07
Drilling

Ahora debemos perforar los agujeros que crearán las conexiones eléctricas dentro del PCB multicapa. Este es un proceso de perforación mecánica que debe optimizarse para lograr el registro con todas las conexiones de las capas internas. Los paneles se pueden apilar en este proceso. También se puede utilizar una perforadora láser para el taladrado.
08
PTH - Plated Through Hole

El proceso de metalizado a través de agujeros (PTH) proporciona un depósito muy fino de cobre que cubre la pared del agujero y todo el panel. Es un proceso químico complejo que debe controlarse estrictamente para permitir un depósito confiable de cobre incluso en la pared del agujero no metálica. Aunque por sí solo no es una cantidad suficiente de cobre, ahora tenemos continuidad eléctrica entre las capas y a través de los agujeros.
09
Panel plating

El plateado del panel sigue al PTH para proporcionar un depósito más grueso de cobre encima del depósito de PTH, típicamente de 5 a 8 µm. La combinación se utiliza para optimizar la cantidad de cobre que se plateará y grabará para cumplir con los requisitos de ancho de pista y separación.
10
Outer layer image

Similar al proceso de capa interna (transferencia de imagen usando película fotosensible seca, exposición a luz UV y grabado), pero con una diferencia principal: eliminaremos la película seca donde queremos conservar el cobre/definir el circuito, para que podamos platear cobre adicional más adelante en el proceso. Esta etapa del proceso se realiza en una sala limpia.
11
Pattern plate

Segunda etapa de plateado electrolítico, donde se deposita el plateado adicional en áreas sin película seca (circuito). Aumenta el grosor del plateado en un promedio de 25um / min 20um a través del agujero. Una vez que se ha plateado el cobre, se aplica estaño para proteger el cobre plateado.
12
Outer layer etch

Este es normalmente un proceso de tres pasos. El primer paso es eliminar la película seca azul. El segundo paso es grabar el cobre expuesto / no deseado mientras que el depósito de estaño actúa como una resistencia a la grabado protegiendo el cobre que necesitamos. El tercer y último paso es eliminar químicamente el depósito de estaño dejando el circuito.
13
Outer layer AOI - Automated Optical Inspection

Al igual que con la AOI de la capa interna, el panel grabado e imagen se escanea para asegurarse de que el circuito cumpla con el diseño y esté libre de defectos.
14
Via hole plugging

Usando tinta de máscara de soldadura o resina epoxi y una plantilla preparada con agujeros que se alinean con los agujeros de los vias que deseamos tapar, utilizamos un proceso de serigrafía para aplicar la tinta o resina en los agujeros. A diferencia de la máscara de soldadura, estamos tratando de hacer pasar la tinta a través de los agujeros en el PCB y evaluamos la calidad con una exigencia de llenado del ≥ 70%.
15
Soldermask

La tinta de máscara de soldadura se aplica sobre toda la superficie del PCB. Utilizando películas de arte y luz UV, exponemos ciertas áreas a la luz UV y las áreas no expuestas son eliminadas durante el proceso de desarrollo químico, típicamente las áreas que se utilizarán como superficies soldables. La máscara de soldadura restante se cura completamente, lo que la convierte en un acabado resistente. Esta etapa del proceso se realiza en una sala limpia.
16
Surface finish

Luego se aplican varios acabados en las áreas de cobre expuestas. Esto permite proteger la superficie y garantizar una buena soldabilidad. Los diferentes acabados pueden incluir Níquel Electrolítico Oro Inmersión, HASL, Plata Inmersión, entre otros. Siempre se realizan pruebas de espesor y soldabilidad.
17
Profile

Este es el proceso de cortar los paneles de fabricación en tamaños y formas específicas según el diseño del cliente, según se define en los datos Gerber. Hay 3 opciones principales disponibles al proporcionar el arreglo o panel de venta: corte con puntuación, enrutamiento o perforación. Todas las dimensiones se miden según el dibujo proporcionado por el cliente para garantizar que el panel sea dimensionalmente correcto.
18
ET - Electrical Test

Se utiliza para verificar la integridad de las pistas y las interconexiones a través de los agujeros; comprobando que no hay circuitos abiertos ni cortocircuitos en la placa terminada. Hay dos métodos de prueba: prueba con sonda volante para volúmenes pequeños y basada en un dispositivo para volúmenes más grandes.
19
Final inspection

Mediante la inspección visual manual y el AVI (Inspección Automatizada Visual), se compara la PCB con los datos de gerber y se logra una velocidad de verificación más rápida que la del ojo humano, pero aún requiere verificación humana. Todas las órdenes también son sometidas a una inspección completa que incluye dimensiones, soldabilidad, entre otros.
20
Packaging

Las placas son envueltas y luego embaladas en cajas antes de ser enviadas utilizando el modo de transporte solicitado.
Durante nuestro horario comercial: 9:00 a 18:00
Contáctanos
Edificios A19 y C2, Distrito N°3 de Fuqiao, Calle Fuhai, Distrito de Bao'an, Ciudad de Shenzhen